How one cosmetics giant’s equipment innovation enhanced safety
How one cosmetics giant’s equipment innovation enhanced safety
L’Oréal’s North Little Rock plant in Arkansas is one of the world’s largest cosmetics manufacturing sites. This article explains how an innovative approach to equipment risks has transformed safety across the whole organisation.
It’s a challenge that those of you responsible for the safety of people at work in industry know only too well: a failure to validate the equipment they use on site can present significant risks and potentially lead to serious incidents. Accidents in the use of equipment are commonplace in work environments, particularly hazardous ones, but the risks are compounded when the machinery is faulty.
Unforeseen defects and malfunctions, exposure to hazardous substances, fires and explosions are among the many and varied types of hazards associated with poorly maintained equipment. It is why validation is a critical step in the journey to ensuring all pieces of machinery meet safety standards and operate as intended.
Consider this challenge, then, for L’Oréal’s North Little Rock (NLR) plant in Arkansas, one of the world’s largest cosmetics manufacturing sites. The NLR factory in central Arkansas is the largest L’Oréal cosmetics location in the world, producing nearly 300 million units in 2022, and the team consists of approximately 650 personnel (450 full-time employees, 125 temporary employees, and 75 industrial subcontractors). The site manufactures mascaras, lip glosses, lipsticks, concealers, cosmetic powders, and nail enamel.
Assessing the risks
The risk assessment is significant. Cosmetics manufacturing involves the receiving, storage, processing, and packaging of components and raw materials and their transformation into products. The NLR plant has over 45,000 square metres of manufacturing capability with significant risks that must be eliminated or controlled. This includes, but is not limited to, process safety, material handling risks, occupational hygiene, musculoskeletal risks, and ‘Life-changing Incident or Fatality Event’ (LIFE) risks (including working at heights, powered industrial trucks, slips, trips, and falls, fire, and hazardous energy).
In this hazardous environment, the workforce operates more than 1,200 pieces of equipment. These include but are not limited to:
- Fixed production equipment (high speed packaging lines, robotics)
- Fixed shop equipment (lathes, mills, drill press)
- Fixed facilities equipment (compressors, boilers, HVAC)
- Portable equipment (pumps, tape machines)
- Flammable liquids processing
- Combustible powders processing
- Overhead doors
- Powered industrial trucks (forklifts, electric pallet jacks, scissor lifts)
- Dock levelers and trailer restraints
- Pallet storage racks.
A new approach
It is of little surprise, then, that the safety team at L’Oréal found that interaction with equipment was a leading cause of near misses. It was a key area of concern that required a new approach and in 2022, the site implemented a new equipment Safety Validation Program. It was, says Travis Ellis, Assistant Vice-President of EHSS (Environment, Health, Safety and Security) at L’Oréal’s NLR site, the key learning point of the year for his team. This was a period in which Travis’s team earned the 2023 RoSPA Sir George Earle Trophy and RoSPA’s International Sector and Manufacturing Sector Awards. “The near miss trending made it clear that a robust safety validation program would be key in preventing equipment-related incidents,” said Travis.
The L’Oréal team’s journey to this award-winning programme involved a deep dive into the evidence. The Group’s policy had been that all equipment is checked and validated prior to use and periodically to ensure the equipment meets specifications and risks are managed, such as machine guarding, electrical systems, and ATEX requirements.
The site has 1,269 unique pieces of equipment that require periodic safety validation, making the historic process difficult to manage. Using trend analysis of equipment-related health and safety near misses or incidents, Travis’s team recognised weaknesses due to lack of standardisation and digitalisation. The process was managed manually and had little visibility across the site.
NLR benchmarked within L’Oréal globally and externally with other Fortune 500 companies to find a sustainable solution. No commercially available system existed that met the site’s requirements and expectations. Therefore, a new third-party system was customised to meet the site’s needs for a robust and standardised process.
Travis said: “We knew that the current process was not sustainable, and that we had to find a digital solution that addressed the weaknesses from our current process to keep our teams safe.
“The site trialed and compared six different platforms for the new safety validation program and selected the third-party system that met all of our requirements, including the capability to trend.”
The new electronic system uses an interactive checklist, QR codes, and proactive email alerts to simplify and expedite equipment safety validation. This system has prevented incidents by standardising checkpoints, enabling more efficient workflows, and allowing deeper trend analysis which decreases the likelihood of safety incidents occurring due to equipment malfunction. The system also provides for traceable corrective actions to prevent recurrence. Overall, the new Safety Validation Program has had a transformational impact.
It had created an internal transformation promoting a more collaborative and transparent relationship between EHSS, maintenance, and operators regarding equipment safety validation. Equipment operators were more engaged as an integral part of the inspection process, said Travis, and had immediate access to the equipment validation status, incident history, and corrective actions.
Due to the increased visibility of deficiencies found during the process, the site has seen a cultural shift from reactive to proactive measures taken to eliminate hazards and prevent accidents on existing and new equipment. Employees at all levels are empowered to recognise and address risks, symbolising the site’s level of interdependence.
“The new system has transformed the safety validation process in NLR,” said Travis. “The process fosters collaboration with various departments and other sites to continually improve the program.”
Sharing the light-bulb moment
NLR's early success was shared with the L’Oréal Zone and Corporate H&S. The simplicity and effectiveness of the electronic system appealed to L’Oréal sites across the globe resulting in Corporate H&S adopting the system as a corporate standard. All 16 sites in North America began implementing the system in 2022 with plans for L’Oréal sites globally to follow. This has the potential to impact over 45,000 L’Oréal employees, reduce administrative work by 57 per cent, and reduce near misses by 40 per cent.
Malcolm Staves, Global Vice-President Health and Safety at L’Oréal, said: “The Safety Validation Program is one of the most important foundations of our health and safety management system in L’Oréal. It has been part of our culture since around 2005 and has seen several evolutions since.
“The work to digitalize this process is a real game changer for us and will help both EHS professionals and line management be more efficient and give them back more time to be on the shop floor interacting with employees. Our NLR factory were curious and innovative enough to see the need and as a consequence all the sites in L’Oréal will eventually benefit.”
More information and support for entering the RoSPA Health & Safety Awards is available here.
Already a member? Login to MyRoSPA to read more articles
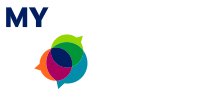
Login to you MyRoSPA account
Login to MyRoSPA to view exclusive member content
Login
| Join RoSPA
Become a member now
Become a member to access MyRoSPA to view more exclusive content
Join
Already a member? Login to MyRoSPA to read more articles
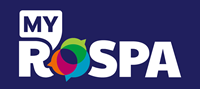
Login to you MyRoSPA account
Login to MyRoSPA to view some more exclusive content
Login
| Join RoSPA
Become a member now
Become a part of the MyRoSPA team to view more exclusive content
Register