How extended realities could transform workplace safety training
How extended realities could transform workplace safety training
In honour of World Day for Safety and Health at Work 2025, which this year takes the theme of 'Revolutionising health and safety: The role of AI and digitalisation at work', Bridget Leathley looks at how VR and AR can be used to train staff to be safer.
‘Extended reality’ or XR is the collective term for immersive technologies which include virtual reality (VR) and augmented reality (AR). Both VR and AR can be viewed through hand-held devices such as phones and tablets or using a head mounted display (HMD). An HMD is more immersive, as the images are on screens directly in front of your eyes, and sound effects are usually played into your ears.
The key difference between VR and AR is that while in VR you can only see the virtual world, in AR images are superimposed on your surroundings – you can still see your feet, and the floor is in the right place!
VR has been around since the 1990s, when HMDs the size of a vacuum cleaner required a large computer and a dark room to operate (and another dark room to lie down to recover from the dizziness and nausea that ten minutes in the experience caused).
HMDs have become smaller and many no longer need to be tethered to a computer to operate. In 2015, leading technology research firm Gartner predicted that VR and AR would reach the ‘Plateau of Productivity’ within five to ten years. Costs have come down, yet in occupational health and safety XR hasn’t lived up to those expectations. We’ll remind ourselves of some of those benefits and look at what has stopped us using XR in occupational health and safety. We’ll finish by looking at the steps to follow to get the best from this technology.
How is XR used in health and safety training?
A key benefit of XR training is to allow learners to rehearse skills that would otherwise be dangerous or expensive (or both) to practice in other ways. For example, confined space training in a classroom can’t get across how it feels to work in a confined space. But training in real confined spaces could expose trainees to the hazards you are trying to avoid, as well as being disruptive to operations. Full scale confined space simulations are expensive and might involve workers travelling to specialist training centres.
In the UK, falls from height are the leading cause of workplace deaths. Employers don’t want to add to the accident toll by training people to recognise damaged scaffolding while relying on it for their safety.
Practicing with real fire extinguishers requires a specialist setup with gas-fed burners if you want realistic fires for people to put out. Each fire extinguisher can be used only once, adding to the expense of the process. It also contributes to your carbon emissions and environmental pollution.
XR can overcome some of these problems, with confined spaces, roof tops and scaffolding modelled in VR, or virtual fires overlaid on your real workplace using AR. Workers can train repeatedly to build competence without additional expenses or real-world risk.
XR has been adopted in high-hazard, high margin industries such as the offshore sector. This highlights another benefit of XR – being able to train someone to work safely offshore while at a training centre onshore. People can work together in the virtual world on a shared task, while in reality spread around the world.
XR allows you to collect a lot more data on developing skills and competencies. How often does the learner select the correct fire extinguisher? How long does it take them to work through the steps needed to operate it? Data analysis also makes it a useful research tool, with the ability to track eye and head movements to see where people look for information such as hazard signs, vehicles or overhead loads.
Another intriguing benefit of XR is that sometimes, we like to learn by making mistakes. What will happen if I use the fire extinguisher at the top of the fire instead of the base, or use the water extinguisher on the electrical fire? How long would I have before I became unconscious if I didn’t monitor the air in a confined space? If the XR experience is well designed it can allow people to find out safely, with the virtual fire responding appropriately, and messages warning you when you would have lost consciousness.
Many studies show that immersive training can be more engaging and increase memory retention compared to traditional classroom or video methods. However, this depends on the quality of the experience, and the opportunity to apply the skills in the workplace.
The opportunities for safety training are not limited to occupational settings. VR is already being used in research to assess the ability of children to make safe crossing decisions compared with adults. Using similar experiences and providing children with feedback could improve the road safety awareness of a generation who have fewer opportunities to learn on their walk to school.
AR can also reduce the need for training. Rather than expecting a maintenance technician to memorise multiple complex procedures, AR can overlay instructions on machinery, providing a step-by-step job aid.
What has stopped the growth of XR in health and safety?
When PC-based e-learning took off at the start of this century, most users already had access to a PC. Although costs have come down, buying HMDs still involves an outlay for equipment you might not use for anything else. And which HMDs should you buy? Key players are Quest from Meta, HTC Vive and Apple Vision, but if you have an XR scenario in mind, you need to check it can work on that headset.
A large organisation can commit to one HMD type and commission a developer to provide bespoke training suitable for the organisation and the hardware. But there is limited material available off-the-shelf for health and safety training, and what is available is spread across multiple platforms.
Although the HMDs are smaller and lighter, and improved visual displays have reduced problems of eye strain, headaches and nausea, some people still find the full VR experience uncomfortable. Interest in AR is expanding, as it overcomes some of the VR barriers while maintaining many of the benefits. For example, instead of a hazard spotting exercise in a cartoon workplace, you can view imaginary spills, obstacles or frayed wires in your own workplace.
How can we get the benefits from XR?
If you are thinking about using XR to provide OHS training, work through these five steps:
- Training needs analysis (TNA): What knowledge, skills and understanding do people need? Are there any concerns about how these competencies are currently provided that could be overcome with XR? Is VR or AR going to provide you with the best solution?
- Test XR Tools: Evaluate off-the-shelf products where they are available, borrowing HMDs if possible. If you are going to have a learning experience tailored to your needs, speak to different developers to make sure they understand your industry, as well as your requirements for data privacy and security. Focus the experience on what people need to learn.
- Involve workers, supervisors and trainers: XR is most effective when used as part of a longer training experience, perhaps involving some classroom theory and other practical exercises, so the trainer will need to be on board with facilitating the XR.
- Run a pilot: Start with a single course and a small number of HMDs. Find out what people thought about comfort, the effort required and any frustrations.
- Evaluate and improve: Measure the impact of the training by assessing skill retention, task performance and confidence levels. Use feedback to refine and improve the experience.
If until now you’ve only considered VR and dismissed it because of usability issues, take another look at AR. Done well, it might bring immersive worlds to a lot more workers and improve the value of safety training.
With a first degree in computer science and psychology, Bridget Leathley started her working life in human factors, initially in IT and later in high-hazard industries. After completing an MSc in Occupational Health and Safety Management, she moved full-time into occupational health and safety consultancy, training and writing.
Already a member? Login to MyRoSPA to read more articles
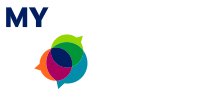
Login to you MyRoSPA account
Login to MyRoSPA to view more exclusive content
Login
| Join RoSPA
Become a member now
Become a member to access MyRoSPA to view more exclusive content
Join
Already a member? Login to MyRoSPA to read more articles
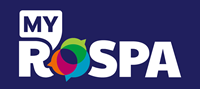
Login to you MyRoSPA account
Login to MyRoSPA to view some more exclusive content
Login
| Join RoSPA
Become a member now
Become a part of the MyRoSPA team to view more exclusive content
Register