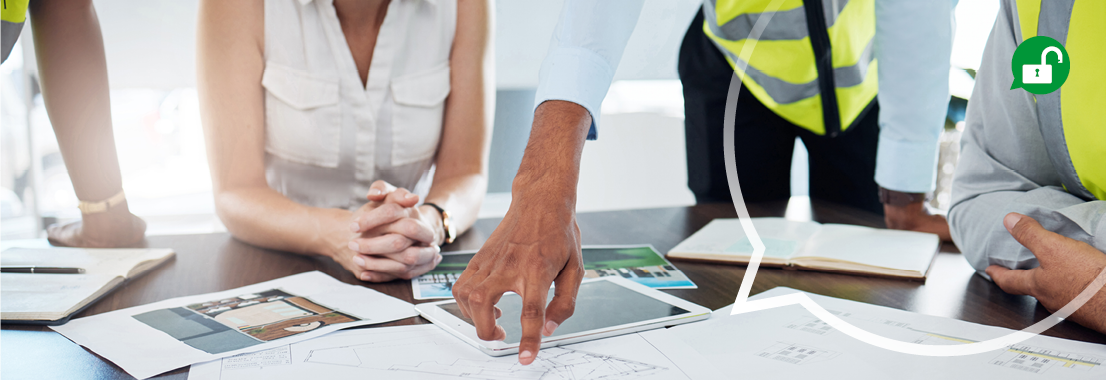
Getting H&S in at the planning stage
Involving safety professionals in the design of facilities and systems benefits the organisations they work for, but it is rare. Louis Wustemann asks how safety practitioners can get in at the planning stage.
The Private Finance Initiative (PFI), later rebranded as Public-Private Partnerships (PPP), was the main source of public infrastructure funding in the UK from the early 1990s until the 2010s. The model was used to finance the building of bridges, hospitals and schools without adding debt to the public balance sheet. It has drawn widespread criticism for being inflexible to demographic shifts; the multi-decade contracts for the private consortia who built and ran the facilities are still enforceable even if there was no longer a use for them because population changes had left them in the wrong place.
But one of the advantages of having building projects overseen by a construction company and a facilities provider – these represented two legs of the stool in most projects, with a bank forming the third – was that from the start there was a representative of those who would maintain the premises. I remember talking to a senior manager in the facilities contractor which had won the PFI contract to refurbish the Ministry of Defence’s Main Building on London’s Whitehall in the early 2000s. Proudly showing off the new plant room he explained how his health and safety adviser had managed to adapt the design of the heating plant to avoid the need for maintenance staff to work at height using ladders or temporary access equipment.
Six months later at a PFI hospital in South Wales I heard a similar story about the tweaks to the specification of flooring in the wards and corridors to avoid slip risks.
These stuck in the mind because they were rare examples of health and safety practitioners with opportunities to head off hazards at the top of the control hierarchy. They were in sharp contrast to the myriad examples I had gathered of OSH professionals having to control risks year after year that had been baked into facilities or systems they were never consulted on.
Alastair Davey is Programme Director at the International Institute of Leadership and Safety Culture and former Global VP Health, Safety and Environment at food services and facilities management company Sodexo, and a strong advocate of safety by design. He says that the legacy of design without proper safety considerations is most apparent in buildings, where, for example small steps up or down in floor height create permanent trip hazards. “How much would it have cost to keep the floor level?” He asks.
“It might have cost nothing or it might have cost a few thousand pounds but you would lose that much on your first accident.”
The tops of buildings are as often problematic as the bottoms. “The number of roofs that we had to maintain as a facility contractor that didn't have proper access, whether it was to clear snow or just to clean the glass. [The designers] created this massive legacy of risk… The bottom line is that architects do not have safety training,” says Davey.
Beyond the physical
Louise Ward, Safety and Sustainability Director (UK & Europe) at freight company Genesee & Wyoming which owns the UK operator Freightliner, notes the potential for managing down risk at the planning stage goes beyond physical installations: “Very few people in their career will get to design a building or a site or whatever, from scratch, but it could just be taking on a new contract.”
Alastair says that when he was given control of food safety at Sodexo, he realised that most of the risk in the millions of meals prepared by the company every day, was further up the supply chain, so doubling down on the hygiene measures of the farmers and food producers was the critical control and gave Sodexo an exemplary food safety record.
Safety professionals’ understanding of a range of risks and ability to assess the most efficient ways of controlling them is rare in business. There are instances of safety professionals involved in the due diligence stages of contracting to buy new company premises finding irregularities in the records on legionella control or asbestos management, giving their companies leverage to gain hefty reductions in the purchase price.
Making safety part of decision-making
It’s easy to say that health and safety professionals should be in on important decisions, but since they so often are not, how can they get a foot in the door?
Building a reputation for problem solving is not an overnight matter. “You have to think: ‘What’s a little step that I can take to get me closer to this?’” says Alastair. He suggests broadening the group of people who are involved in investigating causes after a workplace incident or near-miss. Seeing the kind of thinking that safety professionals bring to evaluating risk and failures, such as fault-tree analysis and the bow-tie method, could give other managers ideas for how those skills could be applied beneficially to business processes.
Louise says that talking to operational people in their own language helps make the case for the value of better risk management at an early stage. Focusing on the precursors of incidents and near-misses and ways to manage them chimes with operational managers, she has found.
“We've talked about leading indicators for years. They're all a bit woolly,” she says. “But if you get into a risk management system, and you really get into your control measures and understand the parameters that they should be operating in, and actively watch for things falling outside the parameters so you can put them back in. Then you're using precursors to optimise your control regime. It's a way of being able to control safety that really particularly appeals to ops and engineering-type people.”
Louise gives the example from her own sector of a precursor to rail accidents: “Having your [track] points lubricated is absolutely critical. So if you're monitoring the amount of points grease you're using and you suddenly get loads more points grease or loads less being used, something's gone wrong with your points greasing, and that can lead to a derailment.”
A voice at board level
For major projects, early intelligence involves having someone in a senior position, preferably on the board, who can flag up developments in the pipeline in time for safety input.
“You need a sponsor,” says Alastair. “You need an ally whose interest it is in to support safety. My first sponsor was the counsel general of the company; he could see safety was going to prevent us suffering legal liabilities.”
Louise Ward agrees; finding an advocate at board level is vital. “Who is it that gets it and can be that advocate?” she asks. “It may be an operational leader, it may be the company secretary, it may be a non-executive director. Often, it's non-execs that get to ask the slightly off-the-wall questions, push a slightly different agenda.”
Of course, the optimum way to be able to influence processes and design so that safety is considered as a fundamental element is not just to secure a senior advocate on the board but to be there yourself. “The advantage I've had in my last few jobs is that I sit as a member of the exec board,” says Louise Ward.
“And that positions safety not as a service that is supporting the business, but as part of designing the future of the business. I'm not there to speak for safety. I'm there to listen, because as we're having those discussions about how the business is going to grow and evolve and what our strategy should be, we can be designing safety in and sustainability too.
“I think it does more than just design out risk, physical risk,” Louise concludes. “I think it sets the tone for your safety culture, and it's that tipping point between having safe operations and safety being designed into business as usual.
“It's safety as an enabler of business as usual, because you're having the conversation at the right stage.”